1. Blow air to keep the soldering iron tip clean. After being powered on, the soldering iron head of the automatic soldering machine is in a high-temperature state for a long time, and its surface is prone to oxidation, which reduces the thermal conductivity of the soldering iron and affects the welding quality. Therefore, in order to increase the lifespan of the soldering iron head of the soldering machine, an automatic blowing function is provided. Impurities on the soldering iron head of the soldering machine can be removed by wiping with a wet sponge. When the temperature is too high, the plug can be temporarily unplugged or dipped in rosin to cool down, ensuring that the soldering iron head of the soldering machine can be well tinned at any time.
2. Tin plating precautions: If there is rust, dirt, or oxide on the surface of the weldment and solder joint, it should be cleaned before welding to facilitate tin plating on the surface of the weldment or solder joint
3. The welding temperature should be appropriate and should not be too high or too low. To ensure a suitable temperature, an automatic soldering machine with appropriate power should be selected based on the size of electronic components. When the power supply of the selected automatic welding machine is constant, attention should be paid to controlling the length of heating time. When the solder automatically disperses from the soldering iron head onto the welded object, it indicates that the heating time is sufficient. At this point, quickly remove the soldering iron head and leave a smooth solder joint in the welding area. If there is no or little tin in the welding area after removing the automatic soldering machine, it indicates that the heating time is too short, the temperature is not enough, or the solder is too dirty; If the solder flows down before the automatic soldering machine is removed, it indicates that the heating time is too long and the temperature is too high. The temperature control of a general soldering iron head is the optimal welding temperature when the flux melts quickly and does not emit smoke.
4. The amount of tin should be moderate. The amount of tin applied to the automatic soldering machine can be determined based on the size of the required solder joints, so that the solder is sufficient to cover the solder and form a suitable and smooth solder joint. Soldering points are not too much tin, it's better to have a lot of tin. On the contrary, this type of solder joint is more likely to be a faulty solder joint, as the solder accumulates on it rather than being soldered onto it. If the amount of tin added at one time is not enough, it can be repaired again, but it must be melted together with the previous tin before soldering; If there is too much tin applied at once, an appropriate amount can be taken with a soldering iron tip.
5. The welding time must be well controlled and cannot be too long. Reasonable control of welding time is also an important part of welding skills. If it is the welding of printed circuit boards. Generally, 1-2S is recommended. If the welding time is too long, it will cause the flux in the solder to completely evaporate, causing the flux to run off, oxidizing the surface of the solder joint, causing the surface of the solder joint to be rough, black, not shiny, with burrs or flow. If the welding time is too long and the temperature is too high, it is easy to burn out the copper foil of components or printed circuit boards. If the welding time is too short to reach the welding temperature, the solder cannot be fully melted, affecting the wetting of the flux and easily causing false soldering.
6. Remember not to touch the solder joint with your hands or shake the solder pad before it solidifies. One is to prevent burns, and the other is that touching and shaking the solder pad before solidification can cause deformation of the solder joint. In mild cases, the solder joint may not look good, and in severe cases, it may cause false soldering. Therefore, during the welding and removal process of the soldering iron head of the soldering machine, it is necessary to fix the solder piece properly, such as using fixtures or blowing air after the soldering iron head is removed, to shorten the solidification time of the solder joint.
7. After a solder joint is welded, the selection of the evacuation angle of the soldering iron head of the soldering machine is also particularly important. Evacuate the soldering iron head of the soldering machine diagonally upwards, and a small amount of solder beads will be taken away from the soldering iron head, forming a smooth solder joint; When soldering machine
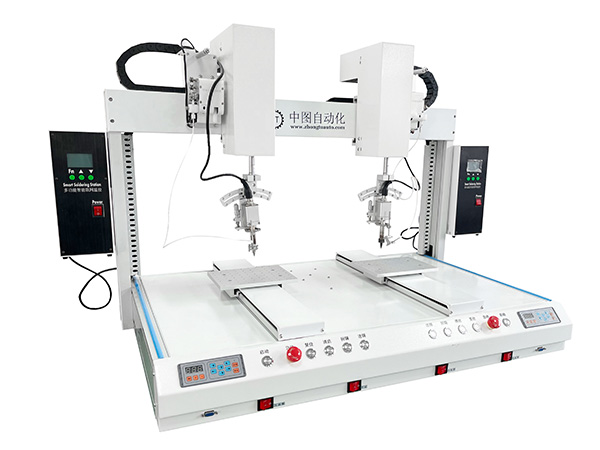